Insights on Conductive Plastics
Overview
Most plastics are inherently electrically insulating materials, they do not conduct electricity. In some applications, imparting electrical conductivity adds significant value and utility. For example, imparting electrical conductivity to plastics enables electrostatic painting in automotive bumpers, reduces dust collection of household molded articles, and facilitates fabrication of some types of plastic films; reducing “telescoping” or the creation and storage of static electricity. Electrically conductive plastic compounds are used as jacket coverings for high power transmission cables; reducing induced currents from nearby cables. Additionally, electrically conductive plastics are used for shielding sensitive electronic components.
There are three regions of electrical conductivity in plastics; 1) anti-static, 2) electrostatic dissipation (ESD) and 3) electromagnetic dissipation (EMI.) Antistatic applications involve materials that exhibit surface resistivity of 10^12 to 10^6 ohm-cm, ESD applications involve imparting sufficient conductivity to plastics to reduce their surface resistivity to the range of 10^6 to 10^4 ohm-cm. The EMI range is below 10^4 ohm-cm.
Sterate additives are typically used to achieve anti-static performance levels. Carbon black and specialty additives are frequently used to achieve ESD performance. To achieve EMI performance metal powders or wires are needed to achieve this level of conductivity. This Modern Dispersions insight article will focus on compounds used to achieve ESD performance and the importance of dispersion on achieving electrical conductivity.
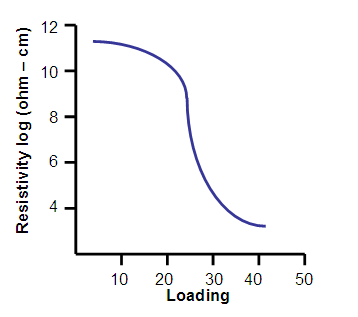
Factors influencing conductivity
A variety of factors influence conductivity of plastic compounds including, the inherent conductivity of the plastic, the level of dispersion achieved for the conductive additive, the intrinsic conductivity of the additive, and the applied electric potential. In the case of anti-static compounds, the conductive mechanism is surface conductivity through bridges formed between water molecules that are absorbed onto the polymer surface, enabled through the use of surface active agents like glycerol derivatives.
For ESD performance, carbon black is frequently used as the active ingredient and conductivity is achieved by forming conductive bridges through a “conduction zone” of overlapping electronic structures, enabling transfer of electrons. Consequently, to achieve conductivity using carbon black, there needs to be sufficient carbon black present so as to form conductive bridges for the electrons.
Percolation: When used to impart electrical conductivity to plastics, carbon black exhibits a phenomenon known as percolation – where the level of carbon black is sufficient to cause a significant and abrupt increase in electrical conductivity. As the loading of the carbon black in the compound increases, the plastic compound remains initially insulating, as the loading increases the conductivity passes through a sharp and abrupt rise over a very narrow black concentration (loading) range. Further increases in loading past this threshold cause little increase in the conductivity. This narrow range is known as the percolation threshold.
Structure influences conductivity: Carbon black structure, surface area, and loading have significant influences on the compound conductivity. The Janzen equation, a widely used model, can be used to predict the percolation threshold concentration based on the density and structure (CDBP) of a carbon black.
The Janzen equation is shown as follows: ϕcrit = 1 / (1 + 4 ρυ)
- ϕcrit = the critical volume fraction (threshold concentration)
- ρ = density of carbon black
- υ = the DBP absorption on the crushed carbon black expressed in cm^3/g.
The conductivity efficiency of carbon black is a function of primary particle size, structure, and porosity. Small particle size blacks have high surface area and higher interaggregate attractive force which result in agglomerates and a pseudo “secondary structure.” Consequently, the pseudo-structure results in higher conductivity than would have been predicted based on the intrinsic structure of the nascent carbon black. However, this secondary structure can cause a reduction in mechanical property and an increase in melt viscosity.
An ideal carbon black compound for industrial users should have the following desirable attributes:
- low percolation threshold (efficiency)
- minimal degradation of mechanical properties
- minimal effect on compound melt rheology
- low compound moisture absorption (CMA)
- cost effective
Achieving the desired balance of properties frequently involves compromises.
Importance of Dispersion Quality
Considering that ESD conductivity is achieved by creating bridges among the conductive additives, a high quality dispersion is essential to distribute the conductive additives homogeneously within the polymer matrix and maintain the balance of properties desired by the end-use application. Carbon black loadings of over 20% are frequently needed to achieve ESD performance in most thermoplastic resins. At this loading level physical properties of the polymer are frequently compromised, thus, the selection of the right carbon black to impart conductivity but not compromise properties or processing is critical. Skill and knowledge, achieved through years of experience, are essential in developing the appropriate compound for the specific resin and specific end-use application.
Modern Dispersions offers a family of products for the static dissipative and conductive plastics markets. Our products are marketed under the Real-Stat® brand. For more information on our products, please see: